Aluminum Framing vs. Welded Steel for Industrial Enclosures and Safety Barriers
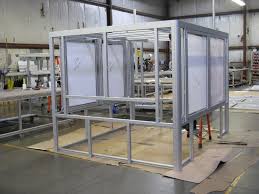
Industrial safety barriers and enclosures play a crucial role in protecting workers and equipment. Choosing the right material for these structures can impact everything from durability to ease of modification. While welded steel has long been a traditional choice, aluminum framing is gaining traction as a flexible, lightweight, and corrosion-resistant alternative. Understanding the strengths and weaknesses of both can help in making the right decision for industrial applications.
Versatility vs. Rigidity in Adapting to Changing Safety Needs
Workplaces evolve, and so do their safety requirements. Fixed welded steel structures may offer initial strength, but they lack adaptability when modifications are needed. Any change in layout or additional enclosures often requires cutting, grinding, and welding, making adjustments labor-intensive and costly.
Aluminum framing, on the other hand, is designed for modularity. Its t-slot system allows for quick reconfiguration without requiring specialized tools or extensive labor. Whether adding extra sections, adjusting heights, or integrating new components, aluminum frames can be modified on-site with minimal downtime. This level of versatility ensures that safety barriers and enclosures remain effective as work environments and operational needs shift.
Lightweight Strength vs. Heavy-Duty Bulk for Industrial Use
Steel has long been valued for its sheer strength, but that strength comes with significant weight. Heavy welded steel structures require reinforced floors, specialized transportation, and often heavy machinery for installation. This additional weight increases costs and makes relocating or adjusting barriers a logistical challenge.
Aluminum framing offers an ideal balance of strength and reduced weight. Despite being much lighter than steel, high-quality aluminum alloys provide impressive load-bearing capacity. This makes it easier to install, transport, and reposition while still providing the necessary durability for industrial enclosures. Its lighter structure also puts less strain on floors and support systems, reducing long-term wear and tear on facilities.
Corrosion Resistance vs. Rust Risks in Harsh Work Environments
Industrial environments expose safety barriers and enclosures to moisture, chemicals, and fluctuating temperatures. Steel, while strong, is highly susceptible to rust and corrosion, especially in humid or chemically intensive settings. Even with coatings or galvanization, steel can degrade over time, requiring maintenance to prevent structural weakening.
Aluminum framing naturally resists corrosion without the need for additional treatments. It does not rust, making it an excellent choice for industries where exposure to water, oils, or corrosive chemicals is a concern. This longevity reduces maintenance costs and extends the lifespan of safety barriers, ensuring continued reliability without frequent replacements or repairs.
Modular Adjustability vs. Permanent Structures for Long-Term Flexibility
Fixed welded steel structures provide stability but little room for change. Once installed, they are permanent fixtures that require extensive work to modify or expand. As businesses grow or floor plans evolve, modifying steel barriers means cutting apart welded sections and fabricating new parts, which is both time-consuming and expensive.
Aluminum framing offers a more flexible solution. Its modular design allows for quick modifications without the need for welding or heavy equipment. Adding extensions, repositioning panels, or integrating new features can be done efficiently, ensuring that the system adapts to long-term operational changes. This adjustability makes aluminum an attractive option for companies that anticipate future modifications to their safety enclosures.
Quick Assembly vs. Lengthy Welding for Faster Setup and Modifications
Installing industrial safety barriers shouldn’t take weeks. Welded steel enclosures require precise fabrication, heavy equipment, and expert welders to ensure structural integrity. This process not only increases setup time but also limits the ability to make on-the-spot adjustments. If last-minute modifications are needed, it often means cutting and rewelding sections, further delaying project completion.
Aluminum framing simplifies the assembly process. Pre-cut sections can be quickly bolted together using t-slot connectors, allowing teams to complete installations in a fraction of the time. No welding, grinding, or painting is required, making it easier to assemble and reconfigure as needed. For industries that rely on minimal downtime, this fast setup process offers a clear advantage.
Sustainable Materials vs. High Energy Consumption in Manufacturing
Environmental impact is a growing concern in industrial construction. Steel production is energy-intensive, requiring significant amounts of raw material and fuel to manufacture. Additionally, steel fabrication generates a high carbon footprint due to the processes involved in welding and coating.
Aluminum framing is a more sustainable choice. Aluminum is highly recyclable, with the ability to be repurposed without losing its strength. The production of aluminum also consumes less energy compared to steel, reducing its environmental impact. Companies prioritizing eco-friendly solutions benefit from using aluminum, not just for its durability but also for its role in sustainable industrial practices.