Exploring the Mechanics of Blast Booth Operations
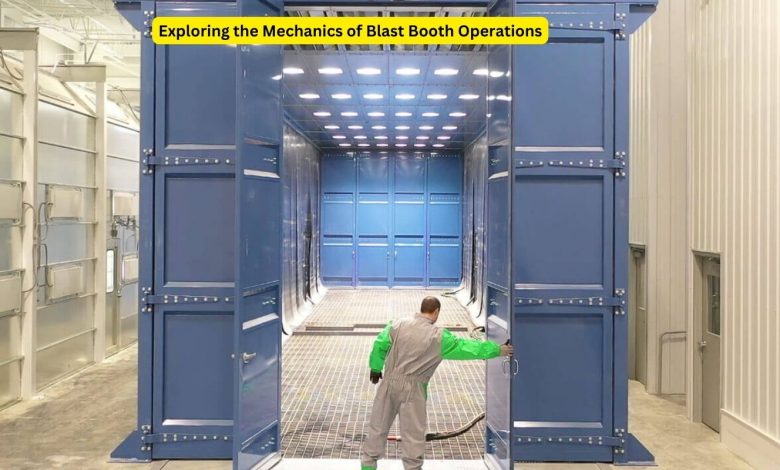
Blast booth are a cornerstone in the industrial finishing sector, critical for the preparation of surfaces that require painting or coating in subsequent operations like those performed in paint spray booths and powder coating booths. This blog post will delve into the functionality of blast booths, outlining their key components, operation, and the integral role they play in ensuring the quality and durability of finished products.
Preparation and Safety Protocols
Before any blasting activity can begin, proper setup of the blast booth is essential. This includes ensuring that the booth is structurally sound, the blasting equipment is correctly installed, and all safety measures are in place. Safety protocols are paramount in blast booth operations. Operators are required to wear appropriate protective clothing, including overalls, gloves, eye protection, and respirators to protect against inhaling hazardous dust.
Preparation also involves a thorough inspection of the equipment. This means checking the blasting tools, the media to be used, and the item to be blasted, ensuring everything is in optimal condition for the task ahead.
Operation of a Blast Booth
The primary function of a blast booth is to facilitate abrasive blasting, a method used to clean and texture the surface of materials. During this process, abrasive materials such as sand, glass beads, or steel grit are propelled under high pressure toward the surface of the item inside the booth. This action effectively removes existing finishes, rust, or other impurities, leaving the surface ideally prepped for further treatment.
The type of abrasive used can vary based on the material of the substrate and the required finish quality. Selecting the right abrasive is crucial as it impacts the efficiency of the process and the quality of the final product.
Ventilation and Environmental Control
An efficient ventilation system is vital in maintaining a safe and operational environment within the blast booth. The system’s design aims to capture dust and airborne particles, filtering them out to prevent health risks and maintain clear air visibility. This not only ensures compliance with environmental regulations but also improves the working conditions within the booth.
Proper environmental control also involves managing the temperature and humidity within the booth, which can affect the performance of the blasting media and the outcome of the surface treatment.
Maintenance and Upkeep of the Booth
Maintaining a blast booth is crucial for ensuring consistent operation and extending the lifespan of the equipment. Routine maintenance tasks include checking and replacing filters, inspecting hoses and nozzles for wear, and ensuring that the abrasive media is clean and uncontaminated. Regular cleaning of the booth itself is also necessary to prevent the buildup of residues that could affect future blasting processes.
Technological Advancements and Future Directions
The field of blast booth technology is continually evolving, with advancements aimed at increasing efficiency, reducing waste, and enhancing safety. Automated blasting systems, precision media control, and more sophisticated recovery and recycling systems are just a few examples of how this technology is moving forward.
Market Trends in Blast Booth Sales
As the demand for effective surface preparation techniques grows, so does the market for blast booths. With a variety of blast booths for sale, potential buyers have a broad range of options, from basic models to those with advanced features and capabilities. The choice of a blast booth can significantly affect the throughput, quality, and cost-efficiency of an industrial painting or coating operation.
Understanding how a blast booth works is essential for anyone involved in the industrial finishing industry. From setup and operation to maintenance and adherence to safety standards, each aspect of a blast booth’s operation is geared toward achieving the best possible results in surface preparation. As technology progresses, these systems will continue to play a vital role in manufacturing, ensuring that products not only look good but last longer and perform better.